Manufacturing Process
Manufacturing Process
Here is the manufacturing process used by our supplier for creating high-quality saw blanks and blades:
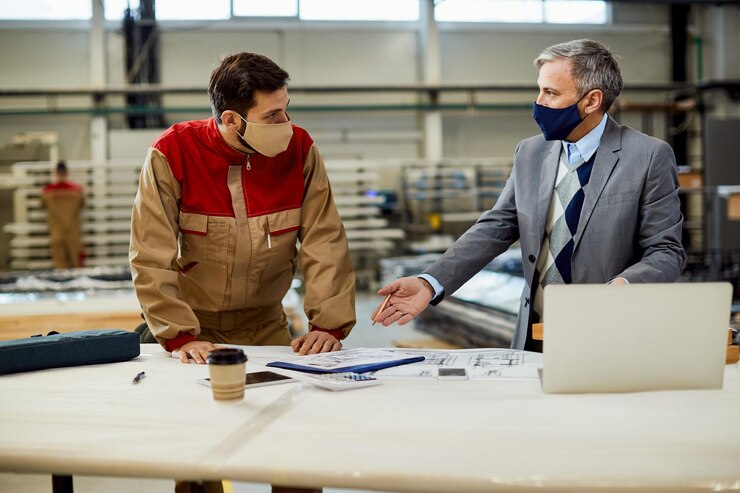
1.
Quality Driven Material Selection
The journey of every exceptional saw blade begins with choosing the perfect steel. For the core of the saw blank, only top-tier steel makes the cut. This high-quality material ensures the blade’s durability and strength, capable of withstanding the intense stresses of cutting operations. By carefully selecting the grade and composition—such as the durable DJ-100 or 75Cr1—Master Saw Blades & Tools tailors each blank to meet specific hardness, tensile strength, and fatigue resistance needs.
2.
Cutting and Shaping with Accuracy
Next, large sheets of steel are expertly cut into precise circular shapes using advanced laser technology. These circular blanks are then meticulously shaped to meet exacting design specifications, ensuring uniformity and alignment. The diameter and thickness of each blank are customized to fit its intended application, laying the foundation for a superior blade.
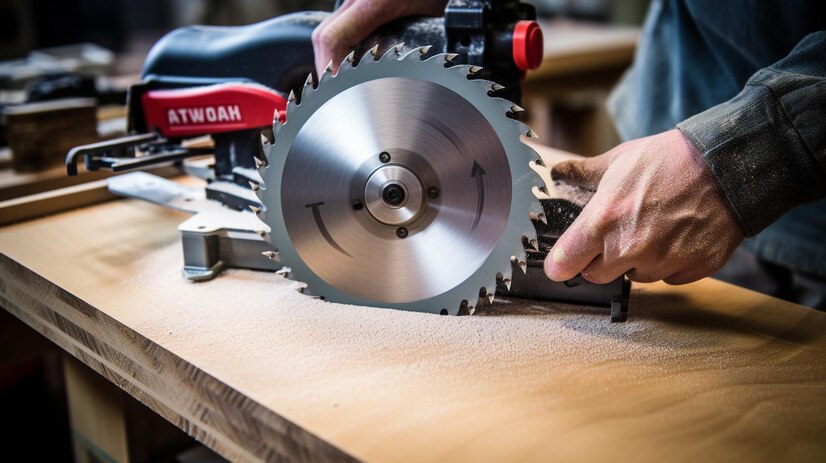
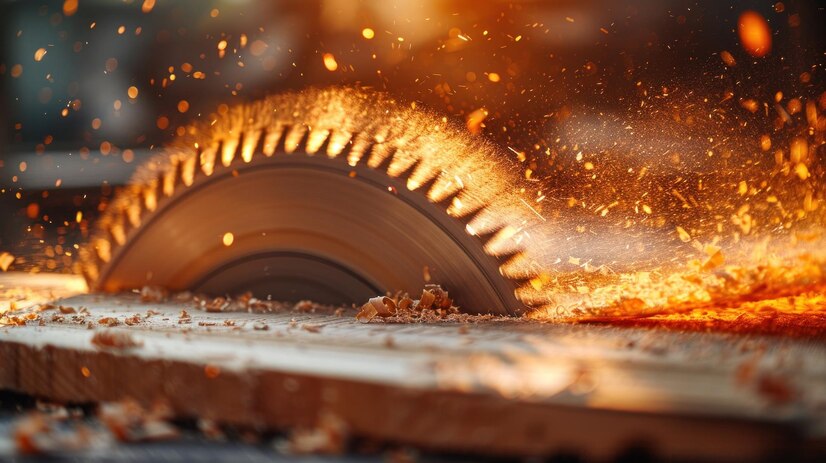
3.
Heat Treatment: Enhancing Hardness
To boost the strength and toughness of the steel blanks, they undergo a rigorous heat treatment process. This involves quenching and tempering, where the blanks are heated to a precise temperature, then cooled under controlled conditions. This process enhances the blade’s hardness, making it more resilient and less brittle—critical for the demanding cutting tasks ahead.
4.
Balancing and Flattening for Precision
Achieving the perfect balance and flatness is crucial for a saw blade’s performance. Through precision surface grinding, each blank is refined to an exact thickness and flatness, resulting in a smooth and even surface. Dynamic balancing ensures that the blades remain stable during operation, minimizing vibrations and reducing wear on the diamond segment.
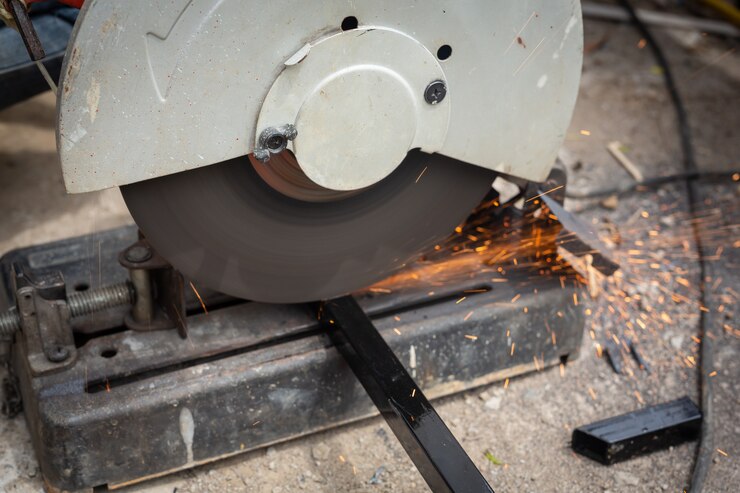
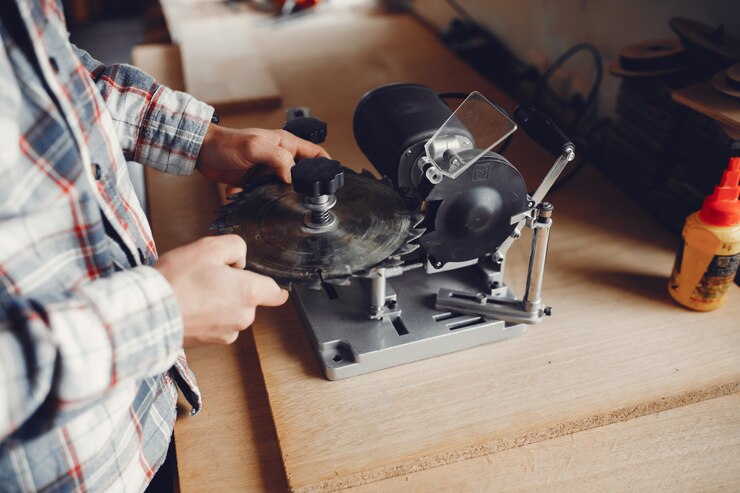
5.
Slotting and Hole Drilling for Performance
To improve cooling and manage thermal expansion during cutting, slots are precisely cut into the blanks. Additionally, cooling holes or patterns are drilled to enhance performance by facilitating better heat dissipation and reducing the blade’s weight.
6.
Surface Treatment: Protection and Enhancement
To protect the steel from environmental factors, some blanks are coated with anti-rust or anti-corrosion materials. Surface texturing or blasting may also be applied, creating an optimal bonding surface for the diamond segments that will be added later.
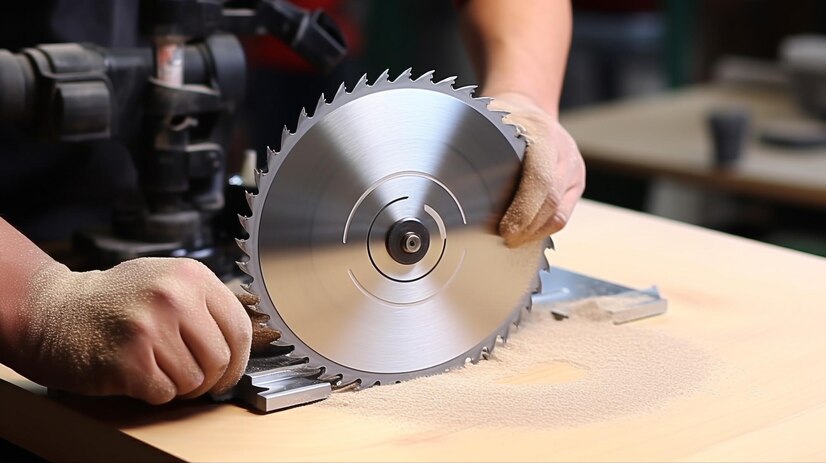
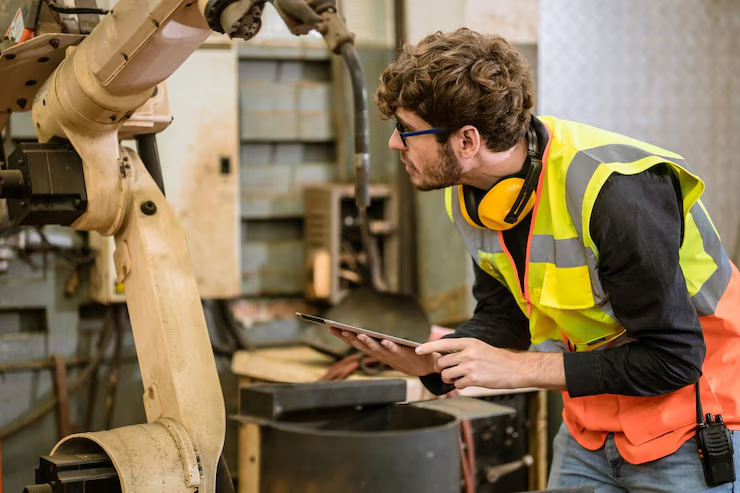
7.
Rigorous Quality Control and Inspection
Quality is non-negotiable. Each blank undergoes stringent dimensional checks to ensure it meets exact tolerances. Further balancing checks are conducted to guarantee stability during use, and ultrasonic testing may be employed to detect any internal flaws, ensuring only the best products move forward.
8.
Final Finishing Touches
The finishing stage involves polishing the edges and surfaces of the blanks to remove any burrs, ensuring a smooth and flawless finish. Each blank is then labeled with essential information, including size, application, and batch numbers for easy traceability.

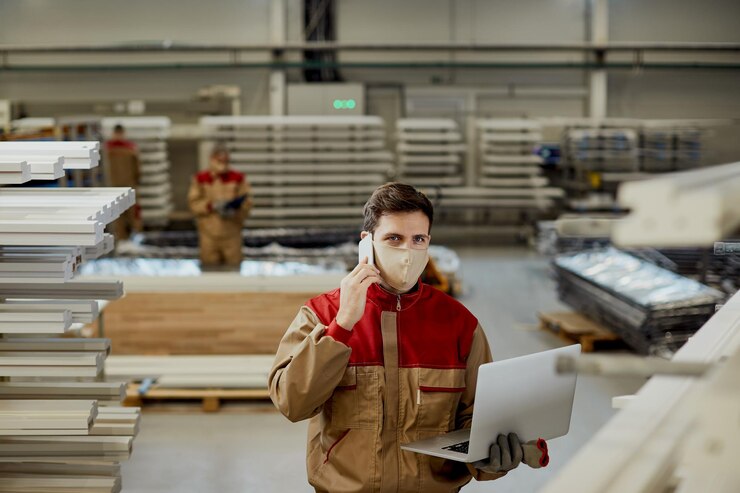
9.
Packaging and Ready for Distribution
Once perfected, the blanks are carefully packaged to prevent any damage during transport. These high-quality products are then distributed to manufacturers who will transform them into fully functional saw blades by adding diamond segments.
10.
Segment Attachment: The Final Transformation for Saw Blades
Although not part of the blank manufacturing process itself, the final transformation into a saw blade involves attaching diamond segments to the steel core. This is done through brazing or laser welding, combining the unmatched cutting power of diamond crystals with the precision-crafted steel core.
This meticulous process ensures that every saw blank and blade supplied by Master Saw Blades & Tools meets the highest standards of performance and durability, ready to tackle the toughest cutting challenges.
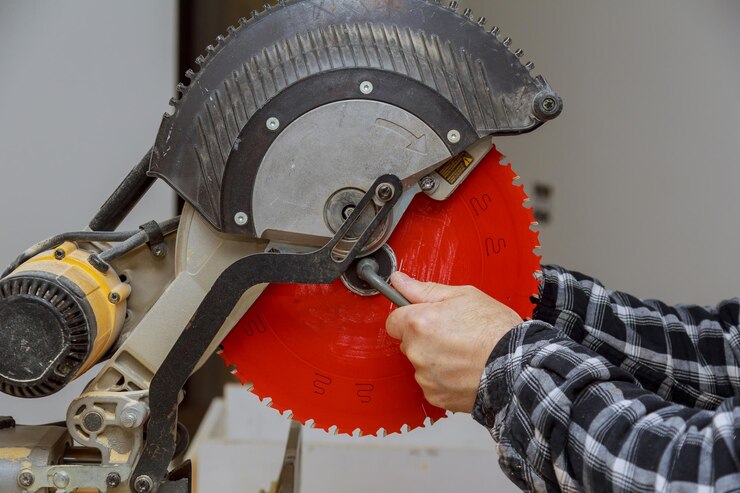
Choose Our Masterful Product Range!
Explore our range of expertly crafted saw blanks, blades, and segments, and elevate your projects with tools designed to perform. Discover the difference today!